Multi-Cyclones (Grit Collectors)
What do multi-cyclones do?
Multi-cyclones are used to separate solid particles, known as particulate matter, from the gases in which they are entrained. For example multi-cyclones can be used downstream of a combustion process to separate flyash from flue gas; or downsteam of a rotary or fluidised bed drier to separate sand from hot air.
Particulate matter from combustion is commonly called smoke. The greater the concentration of particles, the denser the smoke. Particles that are white or light grey in colour and cause white/grey smoke are typically comprised of ash whereas particles that contain unburned carbon are black and appear as black smoke:
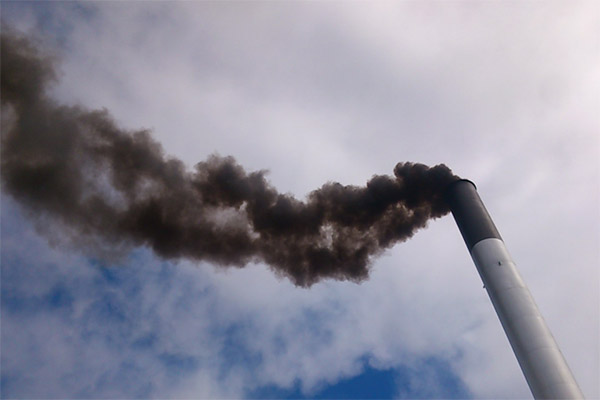
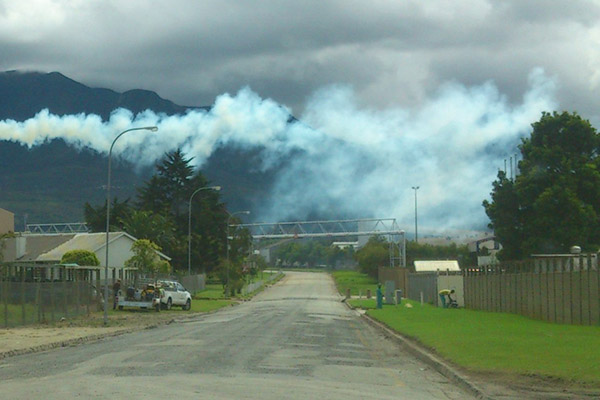
The same stack emitting black smoke (unburned carbon) and white smoke (ash) in the Western Cape, South Africa.
Why are multi-cyclones necessary?
Because particulate matter is detrimental to human health, multi-cyclones are necessary to remove entrained particles from a gas stream before the stream is discharged to the environment through a chimney stack.
Particles that are smaller than 10 µm in size and especially particles that are smaller than 2.5 µm in size (called PM10 and PM2.5 respectively) are the most harmful to human health. PM10 is sufficiently small to become embedded deep in the respiratory system, and PM2.5 can enter directly into the blood stream by passing through the respiratory system.
From an environmental perspective, particles that are entrained in the atmosphere contribute to smog. Smaller particles remain entrained in the atmosphere for many months. This is why it is necessary to remove these particles from the gas stream before the stream is discharged into the environment.
How does a cyclone work?
A gas stream that contains particulate matter enters a cyclone tangentially, which causes the gas to spin downwards flinging the particles to the side of the cyclone and releasing them at the bottom or apex of the cyclone when the gas reverses its direction. The bottom of the cyclone is sealed which forces the gas to change direction and spiral back up the centre of the cyclone. This is called a vertical reverse-flow cyclone, and is the most common type.
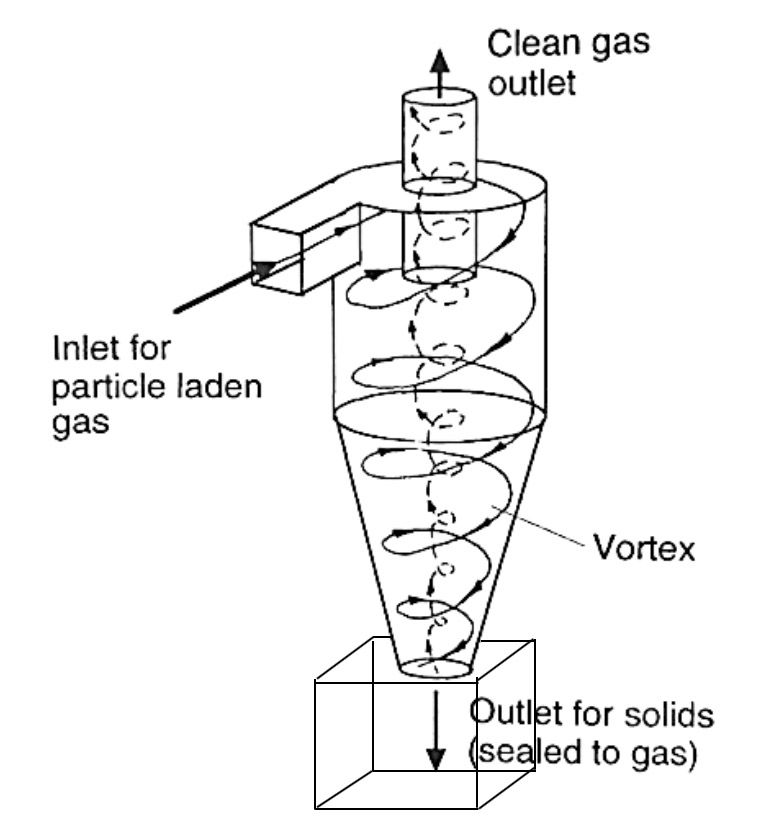
The efficiency of cyclones increases with decreasing cyclone diameter. In order to treat large quantities of gas with a high efficiency it is most effective to group numerous cyclones with small diameters together. This unit is then called a multi-cyclone.
How does a multi-cyclone work?
A multi-cyclone is comprised of many individual cyclones that each use the principles of centrifugal force and inertia to separate particulate matter from a gas stream. Often the particulate laden gas enters each individual cyclone within a multi-cyclone through inlet guide vanes, instead of the tangential entry shown in the diagram above. The guide vanes cause the gas to spiral downwards to the apex of each cyclone.
As a result of centrifugal force, the particles in the gas move radially towards the outer walls and then slide downward towards the apex where they are collected. Near the apex, the clean gas reverses its downward spiral and moves upwards in a second, smaller spiral before it exits from the top of each cyclone. When the gas changes direction, the inertia of the particles keeps them moving downwards, out of the cyclone and into the collection area. This process is shown in the picture beneath and in the video that follows:
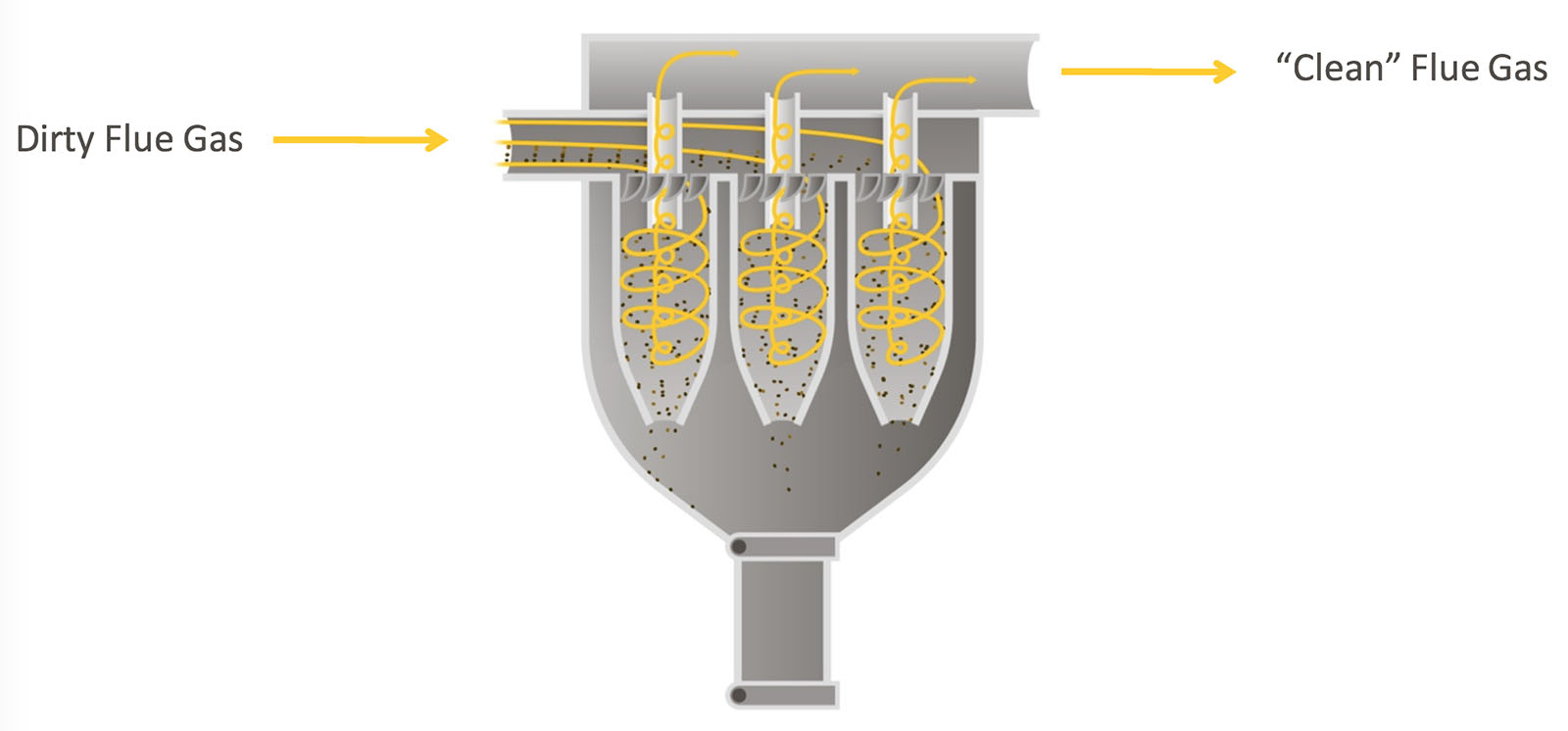
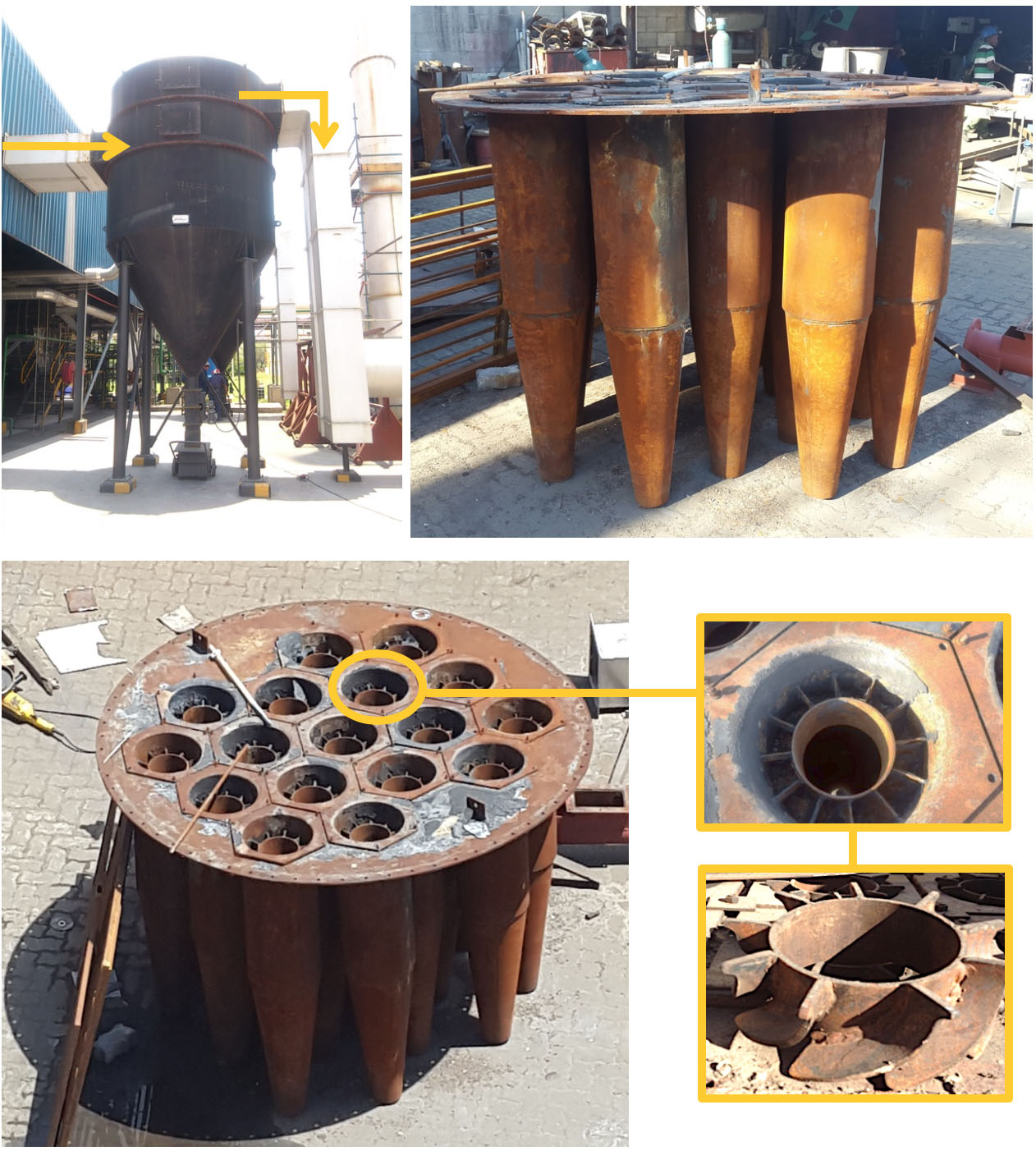
Top Left: An External View of a Multi-Cyclone
Top Right: The Individual Cyclones from Inside a Multi-Cyclone
Bottom Left: The Spinner Vanes on Top of the Cyclones
Bottom Right: Close Up of Spinner Vanes
What are the problems with multi-cyclones?
A broken seal is the most common problem on a multi-cyclone. The cyclones are required to be completely sealed at all times. Multi-cyclones often operate under negative pressure as the induced draught fan is located downstream. Therefore, if multi-cyclones are not sealed at the bottom, air will be drawn in. This air will re-entrain the particulate matter that has collected underneath the individual cyclones, and it will prevent incoming flue gas from swirling cyclonically. This problem is shown in the diagram and video beneath:
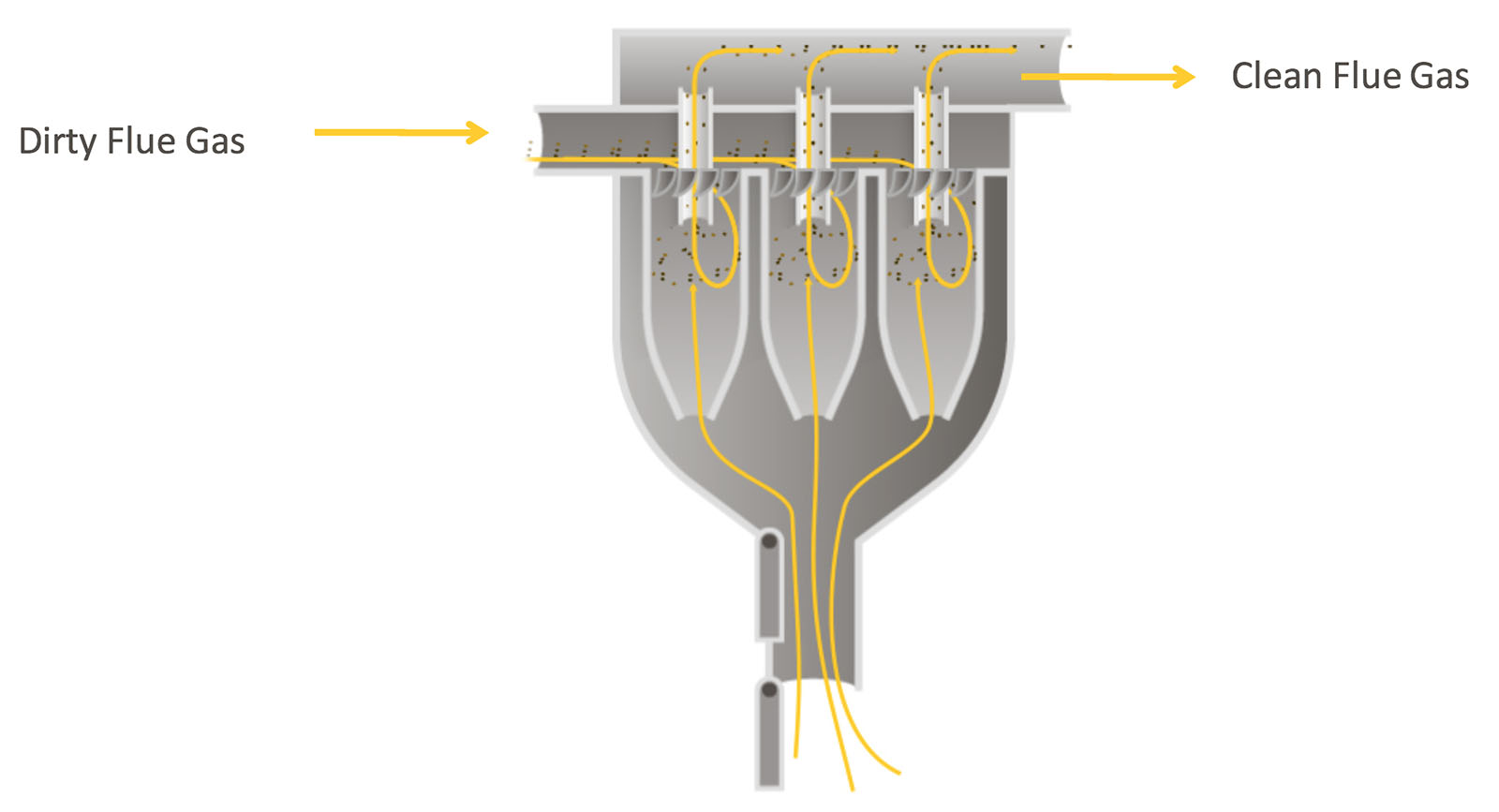
Double flap valves often become stuck open or eroded by particulate matter, as shown in the picture beneath.
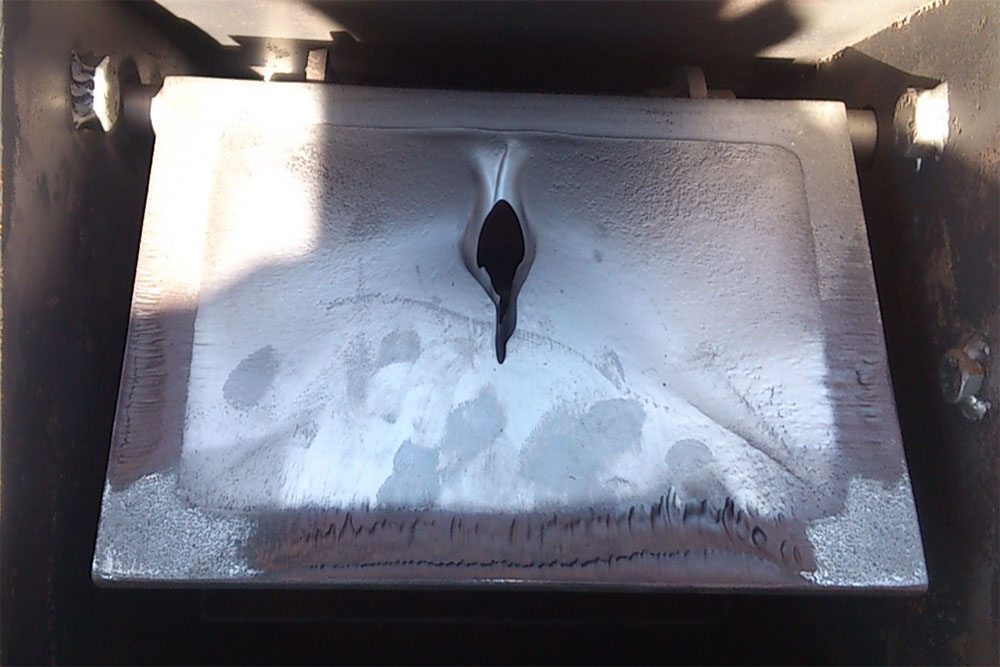
Double flaps need to be inspected daily by the operator to ensure that they are in good working order and sealing well.
Blocked vanes prevent the particulate laden gas from entering an individual cyclone and permit that cyclone to become an exit conduit for air from an adjacent cyclone, thereby increasing particulate matter emissions. This concept is known as intercell flow and is illustrated in the figure and video beneath. It is important to clean multi-cyclones often so as to keep the inlet spinner vanes free from blockages therefore preventing intercell flow.
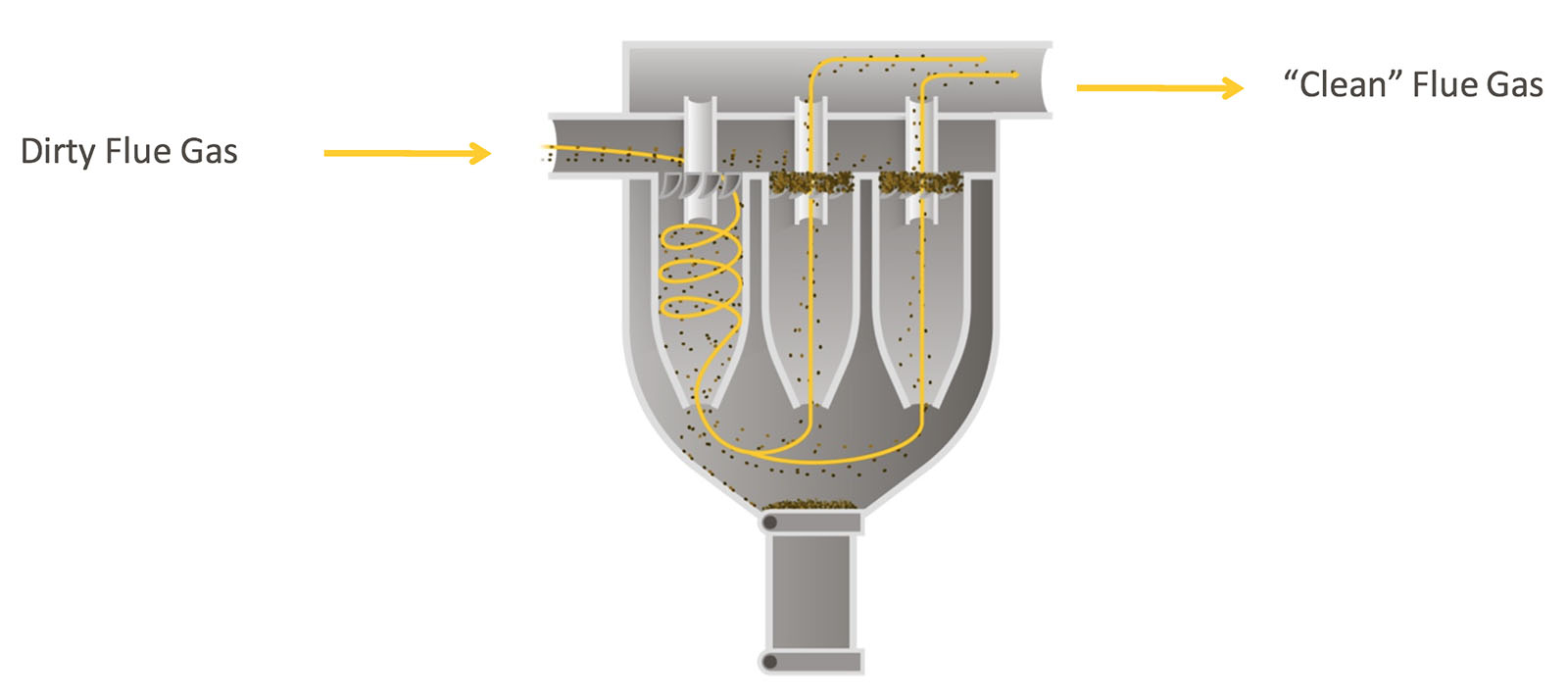
Cyclones erode over time due to the constant swirling motion of the abrasive particulate matter against the cyclone metal. Many boiler multi-cyclones in South Africa were installed thirty or forty years ago, and have not been internally inspected since then. For this reason many multi-cyclones have suffered significant erosion and, in some cases, the internal cyclones no longer exist. The images and video beneath show this erosion and serve to explain why many multi-cyclones no longer arrest particulate matter effectively.
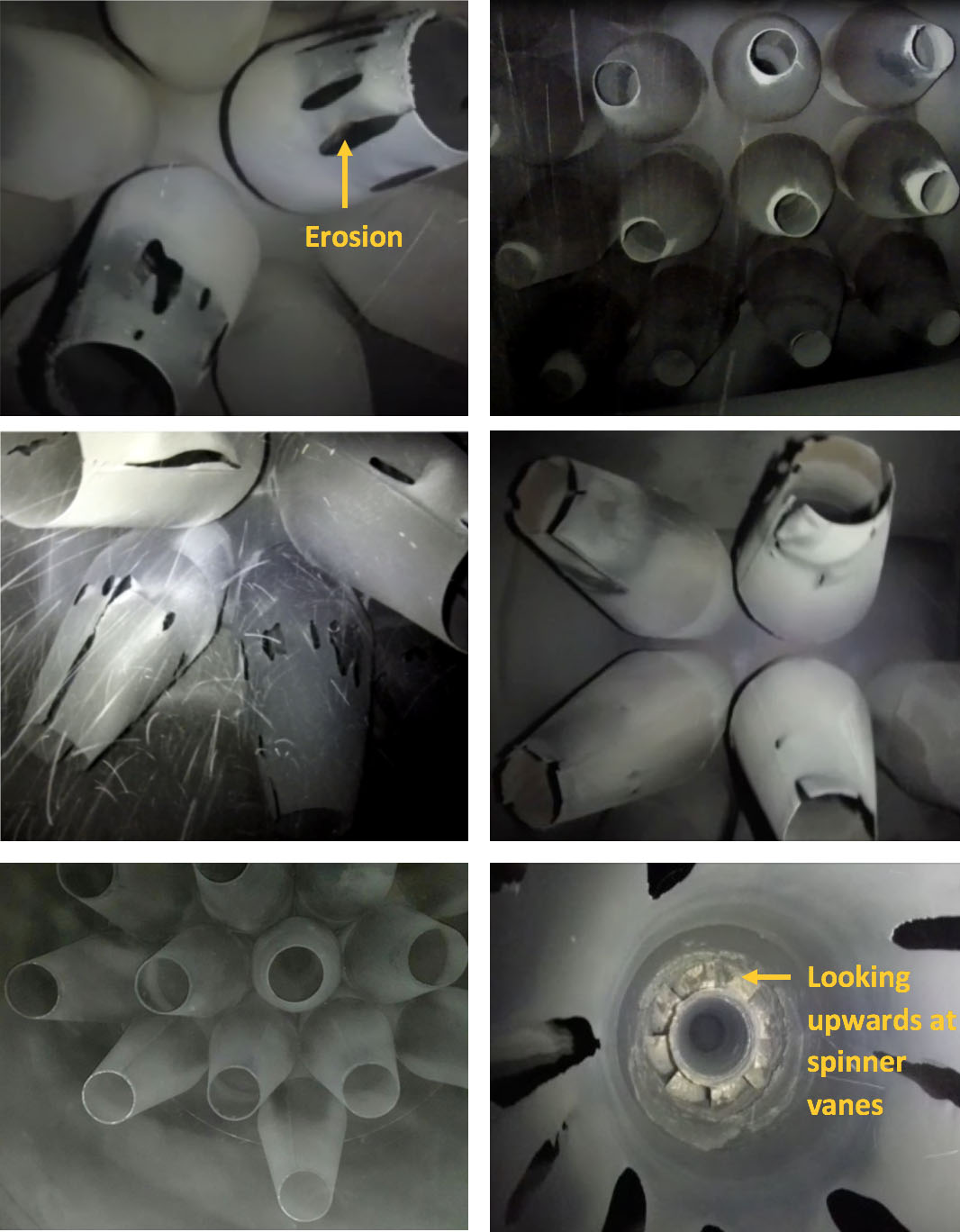
4. Cyclones are Filled with Particulate Matter
Multi-cyclones can become completely filled with particulate matter if the operator does not open the discharge flaps frequently every day. To overcome this problem the discharge flaps on modern multi-cyclones are motorised to open and close automatically. However, on older multi-cyclones these valves must be manually opened and closed. If the operator does not open and close them, the whole multi-cyclone will fill with particulate matter as shown in the video beneath. This is terrible negligence.
Particles are exposed to strong centrifugal forces when swirling inside cyclones, and these forces can cause particles to break down into smaller particles if the particle material has a low tensile strength and is easy to break down (friable). Fly ash has a low tensile strength and is friable. Because boiler emissions consist mostly of fly ash, the use of multi-cyclones on boilers increases harmful PM2.5 emissions.
Therefore although multi-cyclones may reduce the total concentration of particulate matter, they exacerbate the emissions of fine particulate matter (PM10 and PM2.5) which is detrimental to human health.
Multi-cyclones are well suited to applications where particles have a high tensile strength and are not friable, for example the separation of sand or minerals from drying gas streams.
Multi-cyclone performance improves at higher gas flow rates as higher gas flow rates create stronger centrifugal forces in the cyclones and separate more particulate matter. Furthermore, higher gas flow rates cause a greater change in vertical velocity of the gas when it reverses direction at the bottom of each cyclone. However, higher gas flowrates only increase the efficiency of separation up to a point, after which turbulence destroys cyclonic flow and the efficiency of the multi-cyclone decreases, as shown beneath.
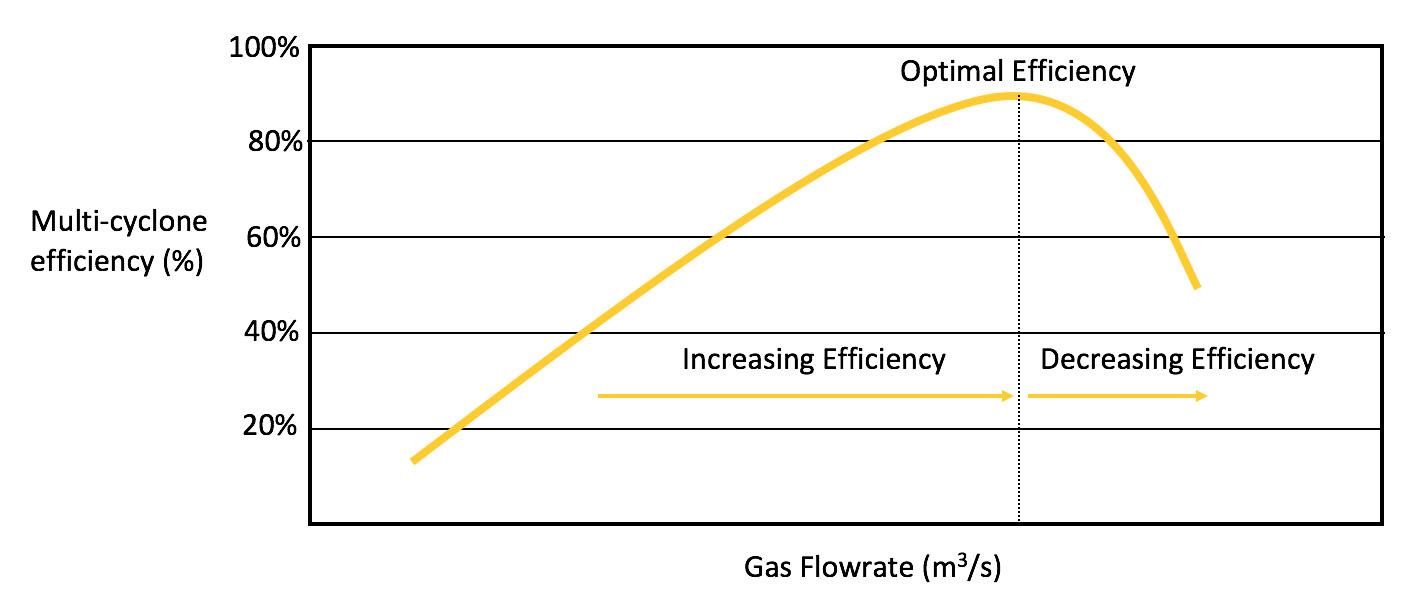
The variable nature of multi-cyclone efficiency is, in Yellow Tree’s opinion, one of the major disadvantages of using multi-cyclones as abatement equipment on boilers which have variable steam demands (and thus variable flue gas flow rates). Multi-cyclones are suited to applications with consistent flowrates so that they can be designed for maximum efficiency at that flow rate.
7. Absolute Performance
a. Concentration
In South Africa, particulate matter emissions from processes and appliances are regulated under the listed activities and controlled emitters legislation. The strictest limit that is imposed upon particulate matter emissions is 10 mg/Nm3, and the most lenient is 250 mg/Nm3. Multi-cyclones may be able to meet the limit of 250 mg/Nm3, but they do not do so consistently. They can not meet many of the stricter limits in the listed activities, such as 50, 30 or 10 mg/Nm3.
b. Particle Size
Multi-cyclones can only arrest particles down to 5 µm in size. Unfortunately multi-cyclones can not arrest the most harmful particles which are smaller than 2.5 µm in size. Furthermore, as discussed above, multi-cyclones create more harmful PM2.5 by breaking larger particles into smaller particles.
What are the advantages of multi-cyclones?
- Cost. Multi-cyclones are available from a wide range of suppliers and are lower in cost than bag filters, electrostatic precipitators, and wet scrubbers.
- Maintenance. Multi-cyclones require very little maintenance. Older multi-cyclones have no electrical components, and besides the sealing flaps, also have no mechanical moving components. Maintenance can be performed with a low level of artisanal skill.
- Space. Although large in size, multi-cyclones occupy a smaller footprint (m2) per volume of gas that is treated (m3) than bag filters and electrostatic precipitators.
- Pressure Drop. The pressure drop over a multi-cyclone is lower than that over a bag filter which means less electricity is consumed by the induced draft fan when a multi-cyclone is being used.
- Easy to Reverse Engineer. By measuring the dimensions of a multi-cyclone exactly, one can build another multi-cyclone with identical performance, without having to perform design engineering calculations. This in turn increases access to technology, and decreases cost; although the ethics of this practice are questionable.
which applications are most suitable for multi-cyclones?
Multi-cyclones are best suited to applications where there is a consistent flow rate of gas that is to be treated and where the particles that are entrained in that gas have a high tensile strength and are not prone to degradation.
Alternative solutions should be sought for processes where emissions are required to be significantly lower than 250 mg/Nm3 on a consistent basis, where it is desired to reduce PM10 and PM2.5 emissions to improve health, where the gas flowrate is variable, and where particles are friable and prone to break down.
What are the alternatives to multi-cyclones?
Bag filters will reduce particulate matter emissions down to ± 15 mg/Nm3. Suppliers normally guarantee bag filters to < 50mg/m3. Bag filters will arrest most PM10 and PM2.5 as they are capable of capturing particles down to 0.2 µm in size.
Bag filters will also easily handle process fluctuations such as deashing, soot blowing, and process flow reversals; eliminating all visible emissions during these unsteady state conditions. Bag filters are a particularly good solution for factories where the stacks receive public scrutiny and where the factory manufactures a well-loved consumer product. For example, the factory beneath is located in a highly visible location next to a prominent sports ground. A bag filter eliminates all visible emissions and preserves the reputation of the brand.
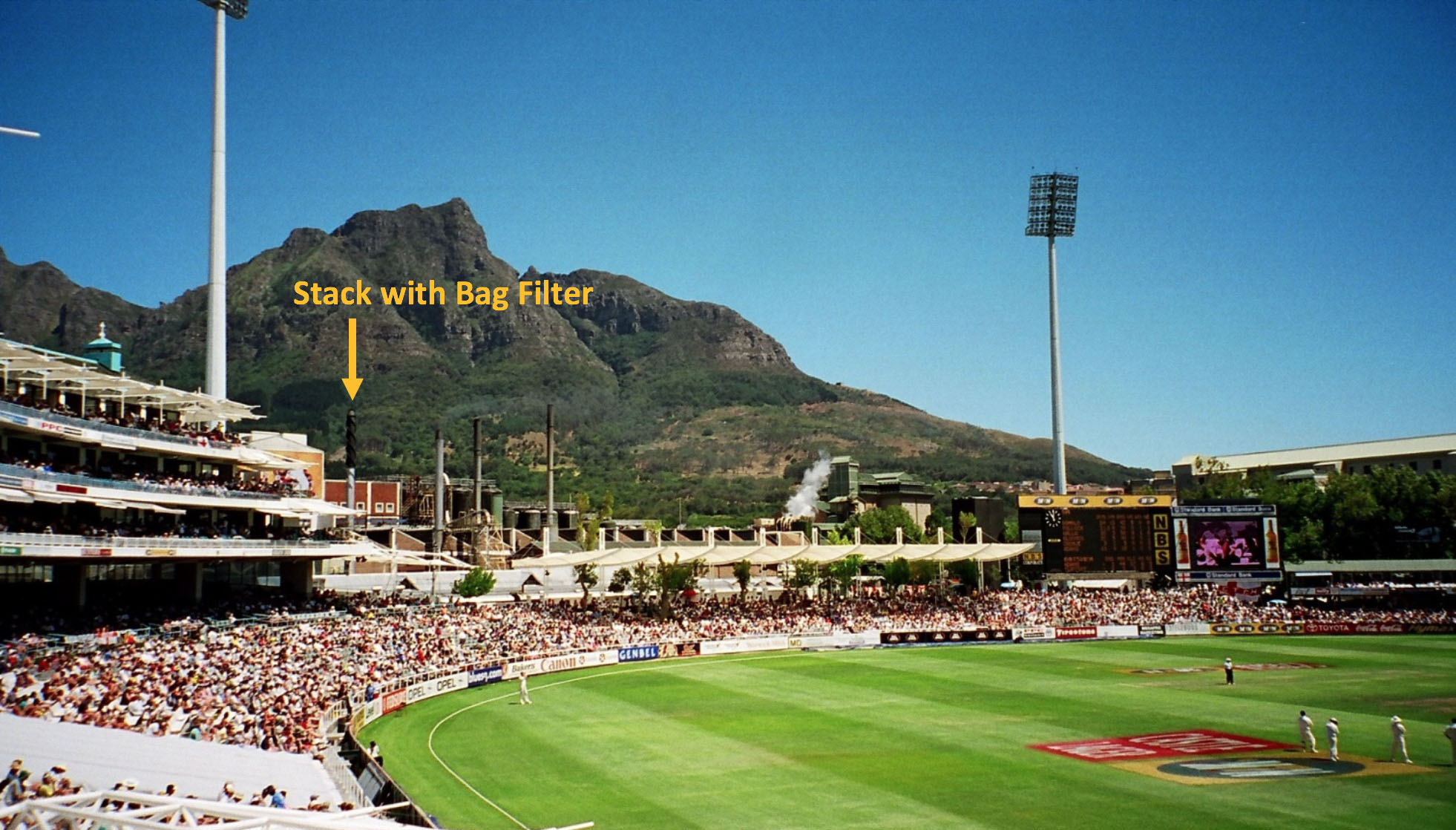
2. Electrostatic Precipitators
Electrostatic precipitators have very little pressure drop as they are essentially large spacious vessels that are packed with plates. The plates are orientated parallel to the direction of flow, and charge and collect the particles. Electrostatic precipitators can be designed to arrest particulate matter down to a user-selected concentration, and can arrest particles down to 2 µm in size.
Electrostatic precipitators are particularly useful when treating emissions from biomass combustion. The particulate matter that arises from biomass combustion is light and fibrous and often burns for a long time. This presents a fire risk to bag filters but not to electrostatic precipitators.
3. Wet Scrubbers
Wet scrubbers are often accused of turning air pollution problems into water pollution problems, but as with all abatement technologies, they are suited to specific applications. Wet scrubbers are very useful when treating other pollutants besides particulate matter, pollutants that are either soluble in water or can be neutralised by a solution. For example, acidic emissions of HF and HCl can be passed through a caustic soda (NaOH) scrubber and converted into harmless salts and water.
Wet scrubbers can be used to treat particulate matter, and at the same time to treat SO2 emissions that often accompany particulate matter emissions on combustion plants such as boilers, because SO2 is highly soluble in water. However, wet scrubbers are prone to corrosion and blockages. Additionally, wet scrubbers create visible plumes of water vapour that the public often mistakes for air pollution.
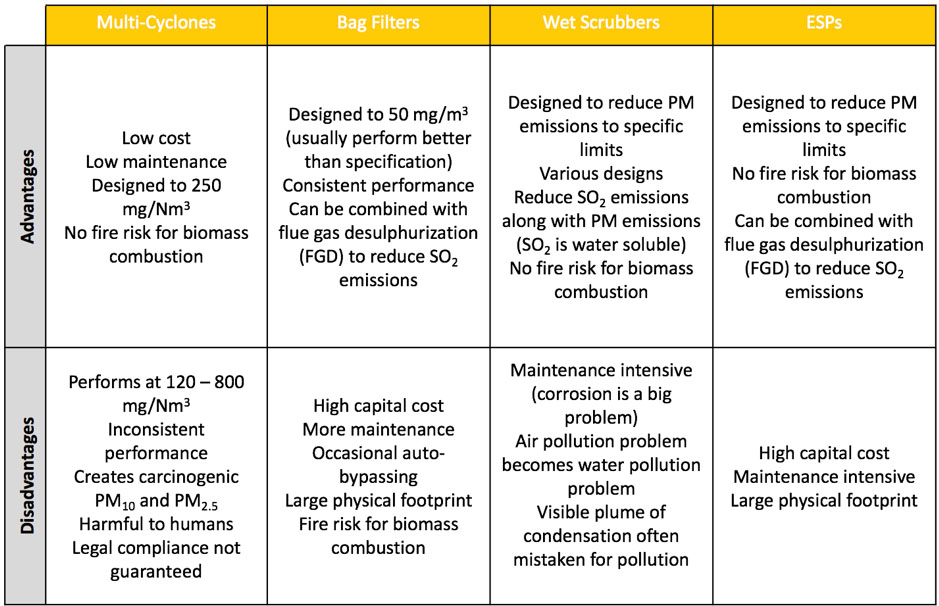
Modern advances in multi-cyclones.
There have been many advances in multi-cyclone technology. The ability to shut off some cyclones and then bring them back online, so as to maintain constant flow through each individual cyclone in the context of a varying overall flowrate, helps to keep the individual cyclones operating at their maximum efficiency. This is an important advance.
Another way of achieving the same outcome, is to recirculate a stream of gas from downstream of the multi-cyclone to upstream of the multi-cyclone, to stabilize the flowrate through the multi-cyclone when the process flow is erratic.
Lastly, there are many different geometries of cyclones, all suited to different particle geometries, flowrates, and inlet concentrations. These geometries continue to be optimised.
In spite of these advances there is no substitute for choosing the right technology for the process application. One should also choose the right technology to meet the emissions limit, while leaving ample margin. If one is aiming to meet a limit of 150 mg/Nm3, then it is prudent to specify abatement equipment that can consistently meet a limit of 75 mg/Nm3 with ease.
A 17 minute tutorial video to supplement your learning from the above article is available at the link beneath, and will cement your knowledge further. Enjoy it!
It is our passion to share engineering knowledge. Please share this article with engineers or SHEQ managers for whom it will be of benefit, so as to develop South African skills, improve the quality of our air and empower one another with knowledge.